Tianjin Bright & Mengde Dairy Co.,LTD
year | category | company | plant | area | industry | movie |
2020 | Consistent | Bright Dairy & Food Co., Ltd. | Tianjin Bright & Mengde Dairy Co.,LTD | China | – | – |
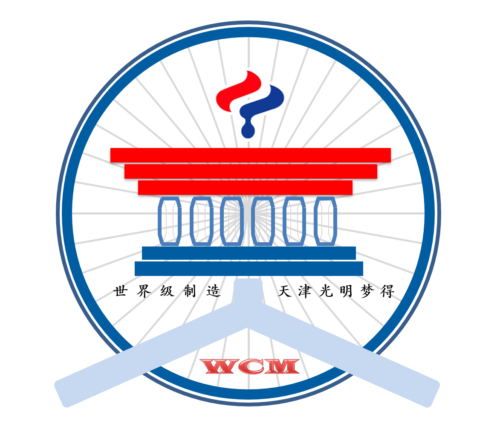
Index.
1. Organization Profile
1.1 Bright Dairy started business at year 1911. The core businesses are the development, production and sells of dairy products. During more than 100 years development, the Group has been the leader of Chinese high-end dairy industry. The Group has world-class dairy academy and use world-class equipment and process to produce fresh milk, fresh yoghourt, lactobacillus, normal temperature milk, normal temperature yoghurt, milk powder, cheese, butter, etc.
Tianjin Bright & Mengde Dairy Co., LTD is a joint venture created in November 2002 which located in Tianjin Beichen Wind Power Industry Zone and covers an area of 100 thousand square meters. It has 352 employees, 12 A3CF filling lines, 3 Fino filling lines and one A3 speed filling line. The total output of the factory was 82.7 k Ton in 2018.
1.2 The process of the factory is divided to processing, filling and distribution. There are three kinds of products including the main product Prisma packed Momchilovtsi yoghourt which accounted for 70% of the output. Therefore, the A3CF filling machine which produce Prisma packed Momchilovtsi yoghourt is the key machine for TPM activity. The management structure of Bright Tianjin factory includes one general manager, one GM assistant who support GM to manage the production, and 8 departments which work together to insure good quality delivery including production, quality, equipment, safety, raw milk supply, integrated management, finance and project departments. Production, quality and equipment three departments run 24h work by three shifts.
2. Milestones on the journey of Manufacturing Excellence
Bright Tianjin factory arrange production according to the production order given by Bright Group. Bright group distribute the total production order to different Bright factory according to their performance of quality, cost and productivity. To improve Bright Tianjin factory business by getting more production order, the factory must improve the general performance including quality, cost, productivity, safety and employee competency. After SWOT analysis, the factory set the vision as to be the performance leading factory in Bright group and determine five strategies as develop people, maximize productivity, high quality, improve cost and ensure safety and low influence on environment. TPM implementation will help factory to achieve these strategies.
3. Benefits Achieved
The factory focused on different improves in different period. During 2014 to 2015, the factory paid more attention on OEE improvement because that the capacity was not enough. The factory had setup several improvement teams including filling machine SMED team and filling machine breakdown reduction teams. In 2016, the factory focused on cost reduction and had setup several improvement teams including package material waste reduction and raw milk waste reduction. From 2017 to 2020, the factory focused on not only cost reduction but also on customer satisfaction.
To improve the ownership of the employees, the factory has setup daily management system. The shop floor was divided to units. The employees from quality, equipment and production departments in each unit recognized as a team and review the performance of the unit together every day and then take actions. Unit leaders review the performance of the entire factory together with supervisors and managers every week. More and more common workers take care of the factory performance. The numbers of persons taking part in daily review increased from 11 to 83. To improve the improvement skills of people, the factory encourages them to join KAIZEN teams. The factory has setup 127 improvement teams in 6 years and 550 persons have taking part in the teams. The factory has collected more than 1235 suggestions, 14895 tags and totally saved 4.8 million RMB. Zero breakdown lines increased from 0 to 4, Zero defect lines increased from 0 to 5. At the very beginning, all the Kaizen teams leaders are managers and now even shop floor workers have the capabilities to be a Kaizen team leader.
4. Key of our Manufacturing Excellence
According to the strategy, the factory finds out the critical success factors. And then divide the CSFs to KPIs. The management committee oversees factory TPM activities and setup pillars to implement. Different employees in different department join in pillars. Each pillar manages its related KPIs. When KPIs achieved, the targets of each department also achieved. So, all employee participation is the recipe of success. Through the participating in interesting activities every year, employees gain happiness in TPM activity. Through internal awards every year, employees gain passion to improve together with the factory. The factory had already won the excellence award category B in 2017 and challenged TPM consistent excellence award in 2020. Then we will continue to improve according to TPM approach, finally, achieve world class level.