Xi’an Yili-Tipco Beverage Company Limited
year | category | company | plant | area | industry | movie |
2020 | Category A | Xi’an Yili-Tipco Beverage Company Limited | – | China | – | – |
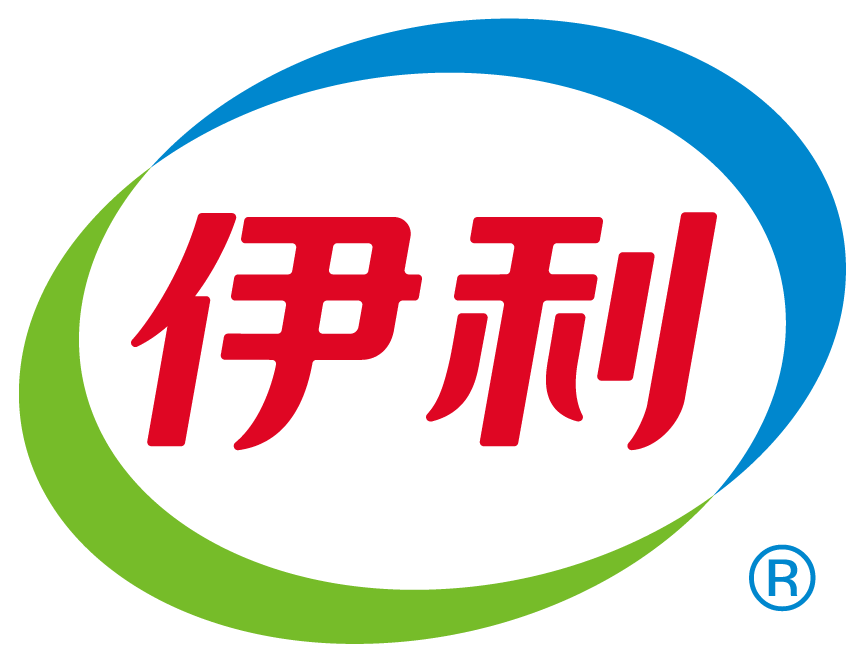
Index.
1. Organization Profile
1.1 Group introduction
Inner Mongolia Yili Industrial Group Co., Ltd. is headquartered in Hohhot City, Inner Mongolia Autonomous Region, China. Yili Group is firmly the leader of global dairy industry, ranking first in Asian dairy industry, and also the largest dairy enterprise in China with the most complete product categories. In the first three quarters of 2020, the gross revenue is RMB 68.677 billion, and the net profit is RMB 5.648 billion.It is estimated that the sales revenue will reach nearly 100 billion yuan in 2020
1.2 Plant introduction
1.2.1 Plant profile
Xi’an Yili-Tipco Beverage Company Limited (address: Gongmao Cummunity, XinFeng Town, Lintong District, Xi’an City, Shaanxi Province, China) was established in 1993 and officially put into operation in 1997. It is one of the subsidiaries of Yili Group. The plant is located at the intersection of G108 National Road and 207 County Road, with an area of 66,700m2 and a total investment of RMB 442 million. It has 22 existing production lines and the output value is RMB 1.82 billion in 2020.
In 2015, the plant officially introduced TPM, taking TPM as the only management mode and promoting it continuously till now.
1.2.2 Product production process
The raw milk of the product is extruded in the pasture and transported to the plant. After passing the test, the following processes are carried out: raw milk receiving → storage → pasteurization → batching → ultra-high temperature sterilization → aseptic filling → packing and other processes. And then the finished products are transported to the market for sale after passing the test.
1.2.3 Main products
The main products produced by the plant are divided into 4 series and 14 varieties, of which the sterilized milk accounts for 49.63% of the total output.
1.2.4 Main production equipment
The plant has 6 types of production machines and 22 production lines, such as two TPA3, four TBA22, five TBA19, four A3-CF, two TFA3 and five TPA1 production lines, with a daily output of 1,200 tons.
1.2.5 Organizational structure
The plant has 10 departments including Production Department, Technology Department, Equipment Department, Personnel Administration Department, Supply Department, Storage and Transportation Department, Safety Department, Finance Department, Energy Department and TPM Promotion Group.
1.2.6 Personnel status
The plant has 631 employees, including 52.8% of production employees, 8.73% of equipment employees, 13.86% of technicians, 39.76% of employees with college education or above and 77.71% of employees with more than 3 years of working experience. The production mode of “three shifts, two on-duties” is implemented.
2. Milestones on the journey of Manufacturing Excellence
2.1 TPM introduction background
With the increasingly fierce competition in China’s dairy market, consumers have higher requirements on product quality, resulting in high complaint rate of products, unstable shelf-life of products and cost of raw and auxiliary materials and labor costs increased year by year. In order to promote steady and rapid development of the plant and realize the vision of “building a world-class healthy food manufacturing plant”, the plant committee formulated the strategy of “improving customer satisfaction, improving profitability, training professionals, and consolidating basic management” in combination with the identification of internal and external environmental factors. In order to support the achievement and continuous improvement of the strategic objectives of the plant, TPM was introduced into the plant in 2015, and the success factors of the strategic objectives were analyzed.
2.2 Plant TPM milestones
In 2013, the plant introduced standardized operations, proposal improvement and QC teams to lay the foundation for TPM development. In 2015, TPM was officially introduced into the plant, and FI and E&T pillars were first launched. In 2016, PM, AM, QM, SH and ENV pillars were launched. In 2018, OM and EM pillars were launched. At present, 9 pillars have been launched. With the continuous development of TPM activities in the plant, TPM improvement culture continues to deepen, and the plant performance has been effectively improved.
3. Benefits Achieved
3.1 Tangible outcomes
Since the TPM was introduced in 2015, the plant OEE has increased by 20.7%,, the number of product complaints has been reduced by 45.6%, and the product defect rate has been reduced by 76%. No food safety incidents or major safety accidents occurred.Due to COVID-19’s influence, the direct material cost of single ton descreased by 7%.
3.2 Intangible outcomes
① Through the effective operation of pillar activities, the cooperation between departments is closer;
② Through the continuous development of group activities, the employee capability has been improved;
③ Employees actively participate in the improvement activities of the plant, with 18 improvement suggestions per capita every year;
④ The plant management system has become more perfect and won the Award for Municipal Excellent Quality Management.
4. Key of our Manufacturing Excellence
① Plant managers clearly regard TPM as the only operation mode of plant management;
② TPM activities are closely related to the plant strategy, which supports the realization of strategic objectives;
③ Integrate the existing organization with the three-level organization of TPM, and involve all employee in the development of TPM activities;
④ Establish a three-level organizational personnel training mechanism to support continuous improvement of personnel capabilities through audit and guidance;
⑤ Establish an incentive system to ensure the active participation of personnel from the three levels of organization.