Sigma Alimentos Sigma Alimentos Lacteos SA de CV, Celaya Plant
year | category | company | plant | area | industry | movie |
2020 | Category A | Sigma Alimentos | Sigma Alimentos Lacteos SA de CV, Celaya Plant | Mexico | – | – |
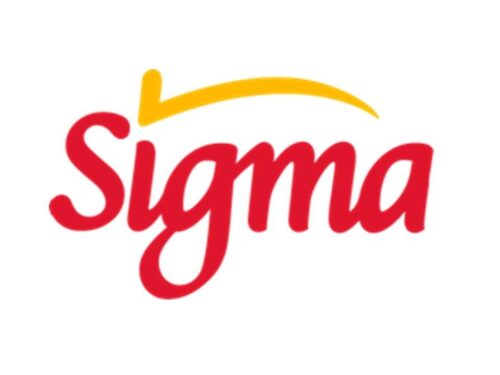
Index.
1. Organization Profile
1.1. The Alpha group is a company whose portfolio of businesses is quite diversified. The roots go back to the end of the 19th century when the first industries were established in Monterrey, Mexico ALFA is integrated by 5 business groups:
• Alpek: Polyester
• Nemak: Automotive industry
• Sigma Alimentos: Food
• Alestra: (Information & communication)
• Newpek (Hydrocarb)
Sigma Alimentos was acquired by Alfa group in 1980 and since then it has grown all over the world through its different categories: dairy products, meats, dry meats and other categories. Sigma is constituted by 70 plants distributed in 18 countries over North America, Mexico and Central America.
1.2 SIGMA ALIMENTOS CELAYA PLANT
Our plant was built in 1977 for “La Mesa” food company; in 2001 acquired for New Zealand Milk Mexico, then in 2005 became part of SIGMA ALIMENTOS CELAYA contributes with 20% of the total volume, produced by all Sigma Alimentos Dairy Products Plants.
Our plant is in the city of Celaya, in the state of Guanajuato, Mexico; strategically located in the center of the country to distribute our products, the plant is built in a land which is 20,000 m2 / 14,000 m2 of construction area.
The Celaya plant is built on one floor, where the different types of cheese are produced. The entire manufacturing of the product depends on manual activities and has the following distribution: 70% corresponds to the production of Panela, 20% Canasto, 10 % Doble Crema.
The graph reflects the total growth in production since 2011 to date in tons and in number of packages. We can see that the trend is towards packages and the growth is pronounced through the years.
ORGANIZATION CHART:
The plant management is supported by the following head departments:
• Education & Training
• Continuous Improvement
Oversees 6 departments:
• Maintenance
• Offices
• Safety
• Production
• Quality
• Implementation
2. Milestones on the journey of Manufacturing Excellence
2.1 The main reason why we acquired TPM in our Celaya plant is that we did not have a solid or organized work team, we had a lot of waste, many of which were not accounted for or measured, we did not meet the service levels, we had machines with very low efficiencies, there were unnecessary expenses, unplanned repairs, constant and costly machine stoppages and the worst part of this is that we did not know how to start acting and even less how to know the root cause.
2.2 We have an artisanal operation with several pieces of equipment with an average of 20 years old, they were not given preventive maintenance, so the losses were uncountable, the personnel did not know their machine and waited for it to be fixed, so the needs of the customers were not met.
2.3 The organization started with high performance teams attacking quality, safety and cost issues, but the results were not so surprising, when TPM and the first pilot teams arrived, a transformation, a structure and a more solid system began, achieving more favorable results.
2.4 There was no loss tree, so the main bottlenecks in the plant were not identified. Thanks to TPM it was possible to identify where the area of opportunity of the Celaya plant and of the different pillars is in order to determine strategies, root cause, methodology and quantify
2.5 In 2013 the TPM Kick off was carried out with 4 autonomous maintenance pilot teams, currently we have 22 teams and we are developing more generations. In addition, we began to integrate multidisciplinary teams for the solution of the main losses of the plant, acquiring experience and anticipating obstacles in the implementation.
2.6 Our Kick Off started in 2013 with the participation of all areas of the plant with great excitement and uncertainty of how we would start working, we have advanced with solid steps in order to continue this wonderful path and now we realized with TPM is not only a management system, it is a different way of thinking. It helps us in an organized and planned way, in such a way that it integrates people, teams and processes in a natural and sustainable way, promotes the development of people’s potential and motivates them to keep improving continuously.
Today, we know there may be many roads, but if we want the best results, continuous improvement with TPM is essential.
3. Benefits Achieved
3.1 In the path of TPM we have observed the way and the actions of the operators using a more technical language, where they already talk about anomalies, unscheduled stops, poka yokes, they have learned to solve problems in an autonomous way where before they did not have such a close contact with the machines and now they are owners of them. The relationship is closer with planned maintenance and quality maintenance, where they share objectives (PQCDSM) and strategies to have more ambitious results.
3.2 The implementation of the methodologies in TPM, knowing the main losses in all the pillars have helped in a favorable way to find the root cause and to be able to continue advancing in the different problems that are put in the future, we continue looking for more ambitious and challenging results.
3.3 We have had many benefits worth showing such as increased equipment efficiency by 43%, quality complaints have decreased by 21%, defaults Saffyc 80.1%, internal defects 77.2%, breakdowns 97.65%, and chokoteis 91.22%. We have much safer areas, as well as the level of service has improved with a positive trend satisfying customer needs.
4. Key of our Manufacturing Excellence
✓ Identification and attention of unsafe conditions in the plant to create a safe and pleasant environment for the personnel.
✓ Ensure objectives alignment from Corporative to Operator level developing Hoshin Kanri, clarifying goals on every activity and why they should be executed
✓ Expanding our loss analysis for manual losses (OHE)
✓ Develop the CBM system to increase the life cycle of the spare parts, to have as a benefit a lower cost of maintenance.
✓ Strengthen the Early Management pillar for the development of new equipment and product processes and thus maximize investments.
✓ Develop skills in personnel to attack complex losses in process for achieve 0 defects, 0 breakdowns and 0 chokoteis
✓ We are committed to developing the skills and knowledge of our employees.
✓ Work in lead time reduction in process, eliminating waste, allows us to increase productivity, capacity, improve cash flow and reduce costs.
✓ Working on sustainability and environment.
✓ Implement and have better tools to address complaints and quality defects on the line, implementing improvement projects to reduce shrinkage and rework.
✓ Continue with the autonomous maintenance steps to maintain and improve its standards to complete these steps and reach the 4 zeros.